83.靠版水辊出现明显跳动的原因是什么?对印品质量有何影响? 产生原因: (1)零件磨损 当靠版水辊摆架内孔或串水辊大铜套出现磨损时认证,或当靠版水辊两端轴座与靠版水辊摆架出现晃动间隙,靠版水辊两端轴承磨损或锈蚀时,靠版水辊与印版接触后,会使靠版水辊产生跳动,必须首先消除这些间隙上海电气,才能使靠版水辊与印版靠实。 (2)设备安装不符合要求 在安装靠版水辊摆架时,没有按照要求安装调隙垫片,致使靠版水辊摆架在印刷时出现晃动。 (3)调节不正确 在印版水分不均匀或脏版时,印刷工以为靠版水辊对印版的压力不足,往往会超常加大靠版水辊对印版的压力唐山玉印,故使靠版水辊产生跳动。 印刷质量的影响: 靠版水辊产生跳动,与印版边口产生撞击,致使印品叼口部位产生脏版,撞击使靠版水辊与串水辊之间产生瞬间滑移,使得印品墨色不匀或形成墨杠。网印 84.为什么正常印刷时串水辊上会粘有油墨?对印刷质量有何影响? 产生原因: (1)串水辊上存在油污包装容器,亲水性能下降。 (2)计量辊对水斗辊、计量辊对靠版水辊、靠版水辊对串水辊压力调节不当。 (3)零件磨损,辊子之间的压力调节后产生变化,压力不合理。 对印刷质量的影响:不利于水分的稳定传递,使版面上水分不均匀。排版 85.润版系统工作不稳定,版面水分不均匀出版印刷,并且水分时大时小,可能的原因是什么? (1)水斗辊、计量辊产生跳动,使传递给靠版水辊的水膜不均匀。 (2)水斗辊、计量辊、靠版水辊内轴承损坏,使辊子转动时出现径向跳动,致使传递给印版的水膜不均匀。 (3)靠版水辊产生跳动防伪印刷,在印版滚筒转过1周时,靠版水辊对印版的压力发生变化,使印版上水膜不均匀。 (4)串水辊上粘有油墨。数字印刷机 86.水辊部分传动面噪声较大的原因是什么? (1)计量辊齿轮、水斗辊传动轴齿轮、中间齿轮的齿面磨损,齿轮间隙增大。 (2)中间齿轮内部轴承磨损,中间齿轮轴磨损。 (3)加工的齿轮网印,齿形不符合要求,齿轮侧隙太大或太小。中国印刷企业强 87.中间辊出现明显跳动的原因是什么? (1)辊子两端轴头磨损或轴承磨损、锈蚀。 (2)中间辊支架内孔磨损,间隙加大,或中间辊支架上的螺丝孔损坏,使中间辊固定不牢。 (3)中间辊对靠版水辊或靠版墨辊的压力调节不当。 (4)靠版水辊或靠版墨辊因调节不当而产生跳动数码印刷机,中间辊跟随跳动。印刷市场 88.水斗辊电机发热的原因是什么? (1)水斗辊产生跳动,与计量辊的压力呈周期性变化,致使电机转动阻力增大而发热。 (2)水斗辊与计量辊间压力太大,电机因转动阻力增大而发热。 (3)加工的齿轮尺寸不符合要求,齿轮的侧隙太小网印,造成水辊电机的转动阻力加大而发热。 (4)电机本身原因造成发热。奥西 89.水斗辊电机发热会造成什么严重后果? 电机发热严重时,会造成电机损坏或使用寿命降低。排版 90.本应该印刷在正面的图案出现在了印品的背面,检查时发现压印滚筒上出现印版上的印记,原因是什么? 正常情况下,印刷机的合压动作是顺序实现的饮料包装,即印版滚筒与橡皮滚筒首先合压,转过一定角度后,橡皮滚筒与压印滚筒合压,其合压动作是在滚筒空当相对时完成的。操作人员在开机时,若按动“开飞达、合压”按钮折页,由于离合压机构出现故障,印版滚筒与橡皮滚筒合压的同时,橡皮滚筒与压印滚筒合压,橡皮滚筒上的图文印在压印滚筒上(此时纸张还在后面的牙排上)。因此,印刷在正面的图案出现在了印品的背面分切,压印滚筒上出现印版上的印记。 产生原因: (1)橡皮滚筒两侧轴套压紧装置对轴套的压紧力太小。 (2)离合压机构中的弹簧顶杆出现故障(例如销轴折断)。 (3)双拉杆机构中的顶丝位置调节不当。收购 91.按动合压按钮后,某机组立即合压,而纸张还没有到达该机组,原因是什么? 可能是因为双倍径滚筒上的光电检测头位置有纸张或表面脏污。如图1所示。展会 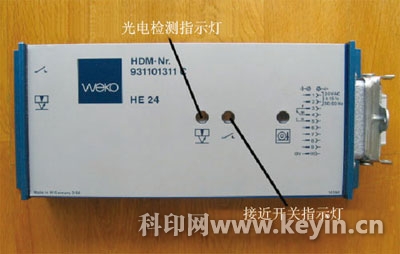 图1 光电检测头人物
92.印刷时,某个色组不合压包装设计,产生这种现象的原因是什么? (1)电磁铁损坏或线路故障。检查方法:扳动机组按钮盒上的合压按钮,若电磁铁不吸合,则电磁铁损坏或出现电路故障。 (2)线路板HE24损坏、接近开关损坏、光电检测头损坏。检查方法:机器每转动1周,线路板上的光电检测指示灯和接近开关指示灯各亮1次,否则可能是上述元件损坏。可以采用与其他机组互换的方式准确判断损坏的元件。 (3)双倍径滚筒上的光电检测头与滚筒表面的距离不正确。 图2所示为印刷压力调节机构图。裁切 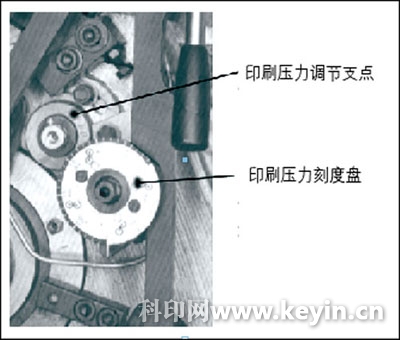 图2 印刷压力调节机构奥西
94.在调节印刷压力时非常吃力,原因是什么? 原因:印刷压力调节支点轴弯曲。 说明:由于牙排之间的交接故障,很多张纸黏附在橡皮布上(尤其是最后机组)套印,异物挤入了压印滚筒及橡皮滚筒中间,印刷压力太大,造成压力支点轴弯曲变形。有时,由于操作不慎,将擦机布掉入机器中个性化印刷,同样会造成压力支点轴弯曲。北人股份 95.收纸链排撕纸的原因是什么?如何解决? (1)收纸牙垫磨损,在收纸链排对压印滚筒进行纸张交接时,收纸牙垫与压印滚筒牙垫之间的间隙太大,交接时出现撕纸现象。 解决方法:更换收纸牙垫,并调节其相对于压印滚筒牙垫的间隙纸箱纸盒,使间隙值达到0.3mm左右。 (2)收纸链排调节不当,闭牙时间太早或与压印滚筒的共同交接时间过长。 解决方法:仔细调节收纸链排。 (3)收纸开牙凸轮磨损后,收纸链排闭牙时间太早或交接时间太长。 解决方法:抽出收纸开牙凸轮上的定位销,调整收纸开牙凸轮的位置,或者补焊修复收纸开牙凸轮政策法规,也可以更换收纸开牙凸轮。 (4)收纸链排两端支座上的链节磨损,链排座中的轴承损坏或磨损、收纸链排的转动轴两端磨损,使得收纸链排的开、闭牙时间不确定。 解决方法:全面修复收纸链排转动轴、修复或更换收纸链排座,对链排座做精确定位。 (5)收纸弧形导轨磨损,收纸链排与压印滚筒进行纸张交接时金融危机,牙排本身出现跳动。 解决方法:更换收纸弧形导轨。 (6)收纸开牙球磨损,导致收纸链排的闭牙时间太早。 解决方法:更换收纸开牙球。唐山玉印 96.收纸牙排与最后色组压印滚筒交接时,发出较大噪声,原因是什么?如何处理? (1)收纸导轨磨损严重,链条与导轨的配合间隙太大;当圆弧导轨磨损后PS版,在收纸链排开牙时,链排出现明显的跳动,发出声音。 解决方法:更换磨损严重的导轨。 (2)收纸链条太松,在链排开、闭牙时及在圆弧导轨换向时发出声音。 解决方法:拉紧链条。如果链条因为磨损而间隙太大,应更换链条。 (3)收纸链排两端支座安装不正利通,链排在导轨中运动时阻力太大。 解决方法:重新对两端的链排座进行精确定位。 (4)收纸导轨安装不当,收纸导轨的间隙太大或太小都会发出噪声;过桥导轨的位置安装不当,同样会发出噪声。 解决方法:按照要求重新校正导轨,当导轨出现明显磨损时,应首先更换或修复。化妆品包装 97.收纸时纸张卷曲的原因是什么?如何处理? 原因:可能没有使用印张展平器惠普,也可能是展平器的吸力不足或太脏。 解决方法:对展平器进行保养,将展平器调整到工作位置,按照纸张的要求调整吸力。失业 98.印品在最后一色组容易上橡皮(剥皮),这是什么原因引起的?如何处理? (1)收纸牙垫磨损,与压印滚筒牙垫之间的间隙太大印后工艺,整个链排或个别牙齿不能叼住纸张。 解决方法:更换收纸牙垫,并调节收纸牙垫相对于压印滚筒牙垫的间隙,使间隙值达到0.3mm左右。 (2)收纸链排调节不当,闭牙时间太晚或与压印滚筒之间无共同交接时间。 解决方法:仔细调节收纸链排。 (3)由于机组间的交接问题,最后一组压印滚筒叼纸尺寸太小区域报道,致使收纸链排叼纸尺寸太小,无法克服纸张与橡皮布间的剥离拉力。 解决方法:首先解决印刷机组间的牙排交接问题。 (4)收纸链排两端支座上的链节磨损,链排座中的轴承损坏或磨损、收纸链排的转动轴两端磨损,使得收纸链排的开、闭牙时间不确定。 解决方法:全面修复收纸链排转动轴、修复或更换收纸链排座,对链排座做精确定位。 (5)收纸弧形导轨磨损供墨,收纸链排与压印滚筒进行纸张交接时,收纸链排本身出现跳动,导致收纸链排叼纸尺寸太小。 解决方法:更换收纸弧形导轨。油墨 99.收纸链条拉长较为严重,在张紧链条时,已经到了调整极限。此现象将造成怎样的后果? (1)由于收纸链条中的连接销轴及连接套出现磨损企业,从而导致链条拉长,当磨损达到一定限度时,销轴的强度下降,尤其是链排两端支座的销轴磨损最为严重。当销轴的磨损达到一定限度时,甚至有断裂的危险胶印,会导致收纸部分产生重大事故。 (2)链条拉长后,链条与链轮轮齿之间的吻合度下降,加速了收纸链轮的磨损,严重时会使收纸链轮的轮齿掉落。 (3)链排两端支座的销轴磨损后,收纸牙排与压印滚筒牙排的交接不稳定展会,造成撕纸故障,并且影响收纸过程的稳定性。组合印刷 |